Take a load off your mind
If your work involves cranes, hoists or the lifting of any type of load, you understand the unique challenges posed by these types of applications. Safety, reliability and productivity are always on your mind. Fortunately, Allen-Bradley® drives are specifically designed to make your job easier. And you can select the type of drive that best meets your needs. AC DC Low voltage Medium voltage.
Put these PowerFlex® drive capabilities to work for you and invest in improved performance
- TorqProve™ Control helps verify control of a load in lifting applications
- Anti-Sway Capability is designed to improve safety and efficiency by reducing the swinging of a moving load
- Regeneration enables a drive to put energy back on the incoming line, providing a braking solution that is far more energy efficient than resistive braking
- Premier Integration is the exclusive experience of integrating Allen-Bradley smart devices into the Logix control environment. It helps you save configuration time and simplify your application
Invest in
When you make the decision to purchase new technology for your lifting application, you’re making an investment in safety, reliability – and most of all, productivity. Moving to application-specific technology can be a big step forward in achieving your goals.
PowerFlex drives provide capabilities that can enhance the performance of lifting applications. Select the drive and capabilities you need.
Patented TorqProve technology helps verify control of a load
When you use PowerFlex drives, you’re getting well-established products that are designed for application flexibility and ease of use.
The TorqProve feature is specifically tailored for applications needing coordinated and sustained control of a load and brake. TorqProve helps to verify control of the load in lifting applications of all kinds. Control capability helps confirm that the mechanical brake has control of the load when stopping the drive, and the drive has control of the load when releasing the brake during any move command.
Combined with excellent low and zero speed performance with accurate torque and speed regulation, TorqProve helps eliminate concerns with brake timing.
It can also help to significantly reduce wear and tear on the mechanical brake with smooth operation and reduced machine stress.
Use TorqProve in any application where coordination between the drive and the mechanical brake is required:
- Cranes
- Hoists
- Draglines
- Material handling lifts (vertical conveyors)
- Automatic Storage and Retrieval Systems (ASRS)
- Palletizer lifts
PowerFlex Drives with TorqProve technology help your application
- Convenient setup, only a few parameters to set
- Brake control is performed by drive
No Special Drive or Software Required
- TorqProve technology is a standard feature of the drive
- The same drive can be used for entirely independent functions on the same machine or in the same This versatility allows you to reduce inventory costs
- Power Flex drives provide high-power capability in a compact footprint
- With the drive controlling the braking, the life of the mechanical brake can be extended
System Performance
- The drive easily integrates via the same communication networks you currently use
- Seamless integration of PowerFlex drives and Logix programmable automation controllers helps increase productivity by providing easy access to system and machine level data and diagnostic information
Anti-sway capability
One major challenge for many lifting applications involves the swinging of a load. Any time a crane moving a load accelerates or stops, it causes the load to sway back and forth. The heavier the load, the more potentially dangerous and disruptive the swinging becomes. Production time is lost while waiting for the load to stabilize when in position. To address these concerns, PowerFlex 755T drives provide built-in anti-sway capability.
Anti-sway capability in PowerFlex 755T drives:
- Helps protect personnel and assets by reducing the unpredictable, pendulum-like movements of a load
- Helps improve productivity by reducing the time needed to wait for a swinging load to stabilize
- Helps control sway of a load without the need for additional sensors, external controller or complex programming
- Doesn’t require application expertise – just configure a few drive parameters
- Helps extend the life of mechanical components
- Can be used with a manual or automatic operation mode
With anti-sway, we can have a higher cycle time because the deceleration is managed by this feature, which allows us to lower the hoist when we arrive at the destination. We don’t have to wait.
The benefits of anti-sway capability also extend to applications that involve the movement of fluids.
Use drives with built-in regeneration capability to help reduce energy consumption
Using built-in regeneration capability, some PowerFlex drives can help reduce energy consumption by putting energy back on the incoming power supply, providing a solution that is far more energy efficient than resistive or mechanical braking. Regenerative drives also help to eliminate the need for braking resistors and cooling equipment along with associated wiring, labor, installation and maintenance costs.
The PowerFlex 755TR drives, PowerFlex 755TM bus supplies, PowerFlex DC and PowerFlex 7000 drives have built-in regeneration capability to help you avoid wasteful dissipation of energy. Instead, use that energy for other applications.
How does regeneration work?
When a load is lifted, energy goes into the motor from the drive, then into the machine from the motor. When this happens, the motor and rotation are in the same direction, meaning the system is operating in a “motoring” or “consumption” mode.
But when the load is lowered, the motor and drive must hold back the load to control its speed. Energy comes out of the machine and into the motor, then from the motor into the drive. When this happens, the motor torque and rotation are not in the same direction and the system is operating in a “regeneration” mode.
The motor behaves as a generator. When the drive is in a regeneration mode, energy flows back onto the mains and can be used for other purposes.
Premier Integration
Premier Integration is the exclusive experience of using Allen-Bradley smart devices in the Logix control environment.
The Studio 5000® environment serves as a single programming tool for the design and configuration of your application. You need only one software package for discrete, process, batch, safety, and drive-based applications.
- Drive configuration is saved as part of the Studio 5000 Logix Designer® project file and stored in the Logix. You only need one file for both the controller and all drive configurations.
- Consolidating controller programming and device system configuration helps reduce complication and eliminates mismatch errors
- Drive profiles provide a visual interface for automatic tag generation, instant pairing of controller to drive, and tools to assist drive configuration
- Diagnostic, fault, alarm and event information are integral to the Studio 5000 environment
Leverage the Studio 5000 environment to manage application libraries
- Rockwell Automation provides libraries of application code that enable you to take pre-built code and apply it to any Allen- Bradley automation device, making set up of the equipment fast and easy
- Application Code Manager enables time savings during commissioning and enhanced productivity by reusing application code independent of automation device platform
Analytics and visualization
Analytics and visualization provide windows into critical production and process information gathered from self-aware and system-aware smart devices like PowerFlex Drives. Enabling you to:
- Predict mechanical problems and help improve performance with diagnostics in real-time
- Investigate, collaborate and troubleshoot in the plant – instantly with no setup and very little change to your infrastructure
- Providea common user experience for all Rockwell Automation devices with pre-engineered faceplates that provide necessary information for engineers, operators, and maintenance personnel
Safety solutions help improve productivity
Integrated functional safety helps to increase productivity in machine operation and maintenance. Safety ratings up to SIL3, PLe, and CAT 4 are available.
- Decreased set-up times for networked solutions compared with hardwired safety
- Diagnostics become more accessible as part of the overall system
- Safety instructions and functions integrate into the controller for modularity and scalability
PowerFlex 755T Drives
Offer harmonic mitigation, regeneration and common bus solutions in a wide power range of 10…6000 Hp / 7.5…4550 kW.
PowerFlex 755T AC drives provide unique benefits
PowerFlex 755T drives are the only VFDs on the market to offer the combination of TorqProve Technology, Anti-Sway Capability, Regeneration and Premier Integration. Using patented technology, they offer a variety of exclusive benefits to help improve the safety, dependability and productivity of your lifting application.
The PowerFlex 755T drives provide harmonic mitigation, regeneration and common bus solutions that help you reduce energy costs, gain flexibility and increase productivity. These are the first drives to offer TotalFORCE® technology to achieve excellent motor control through precise, adaptive control of velocity, torque and position for electric motors. The PowerFlex 755T drives include:
- PowerFlex 755TL Drive – Provides harmonic mitigation and power factor correction through the use of active front end by reducing the adverse effects of harmonic distortion, the drive helps to improve energy efficiency, reduce energy costs and minimize power distribution issues on the factory floor.
- PowerFlex 755TR Drive – Features built-in regeneration capability that helps decrease energy consumption by delivering regenerative energy from motors back to the incoming Line regeneration reduces the need for braking resistors and associated cooling equipment and helps avoid wasteful dissipation of energy. The drive also offers harmonic mitigation.
- PowerFlex 755TM Drive System – Select from a series of predesigned configurations for regenerative common bus supplies and common bus inverters to optimize your system design and power. A common bus drive system offers advantages such as design flexibility, energy optimization and reduced installation costs. PowerFlex 755TM systems provide harmonic mitigation and built-in regeneration capability.
For more information
www.ab.com/Drives
PowerFlex 755T Brochure, publication 755T-BR001
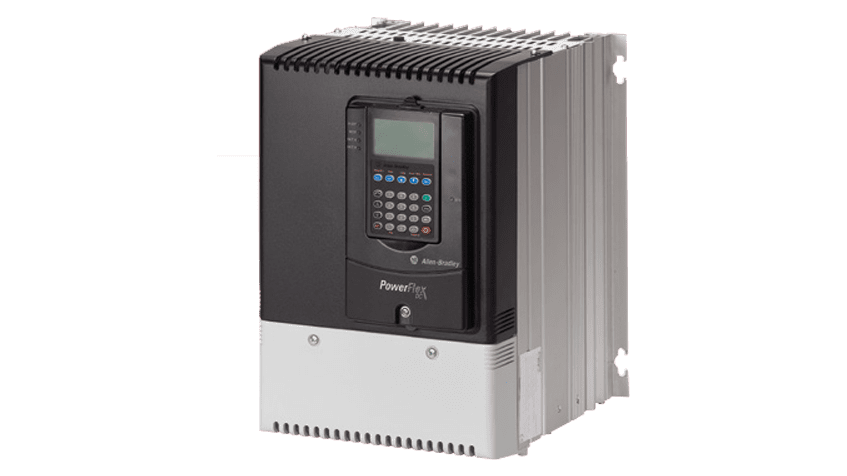
Key benefits of the PowerFlex 755T drives
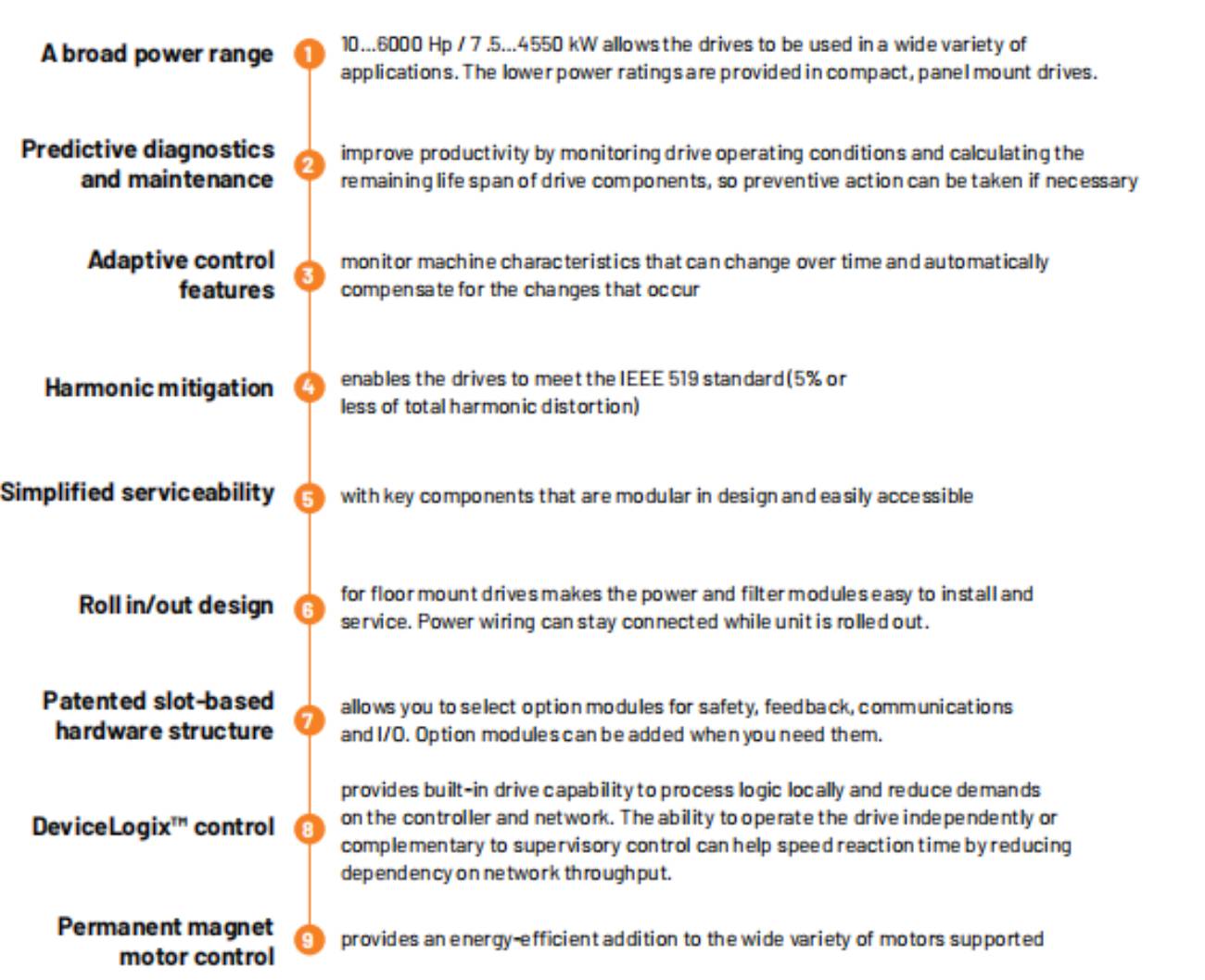
Maximize your productivity
Take advantage of PowerFlex Drives
In addition to providing exclusive features for lifting applications, the robust family of PowerFlex AC and DC drives provide ease of use, flexibility and performance for a variety of industrial applications
PowerFlex 755 AC Drives
With a complete power range of 1 to 2000 Hp (0.75 to 1500 kW), the PowerFlex 755 AC drive supports a wide range of network protocols to simplify integration into your architecture and features an embedded EtherNet/IP port for easy management of drive data over EtherNet/IP networks. To help protect personnel and equipment while reducing machine downtime, the drive offers safety solutions up to and including PLe/SIL3, Cat 3 and Cat 4. Automatic device configuration (ADC) is a productivity-enhancing benefit of Premier Integration and is available when the drive is used on an EtherNet/IP network. ADC enables a Logix controller to automatically detect a replaced PowerFlex 755 drive and download all configuration parameters, minimizing the need for manual reconfiguration.
PowerFlex 7000 AC Drives
The PowerFlex 7000 family of medium voltage AC drives delivers flexibility and highly efficient performance in a single solution for motor control applications from 200 to 34,000 Hp (150 kW to 25,400 kW), rated from 2.4 kV to 6.6 kV. To help protect personnel and equipment while reducing machine downtime, the drive offers safety solutions up to and including PLe/SIL3, Cat 3. Choose a configuration with Direct-to-Drive™ technology– and connect a drive directly to the line without the use of an isolation transformer. Direct-to-Drive technology combines an active front end (AFE) rectifier to lower line- side harmonics and a patented DC link inductor to address common mode voltage at its source. This allows the use of standard motors, making it ideal for both new projects and upgrades of existing applications.
PowerFlex DC Drives
The PowerFlex DC drive combines powerful performance between 1.5 to 1400 Hp (1.2 to 1044 kW), with flexible control to produce a highly functional, cost-effective drive and control solution. PowerFlex DC drive modules are available in both regenerative and non- regenerative configurations and standard IP20 open type enclosure. The PowerFlex DC includes an armature converter, regulated field converter for field weakening or economy applications, an advanced regulator with integrated DPI functionality, DC tachometer and encoder capability. Unlike many other DC drives available today, the PowerFlex DC can be easily integrated into your complete manufacturing system. With drive profiles for Premier Integration, end users can now have a single software approach to configure their controller, drive system, and for operation and maintenance.
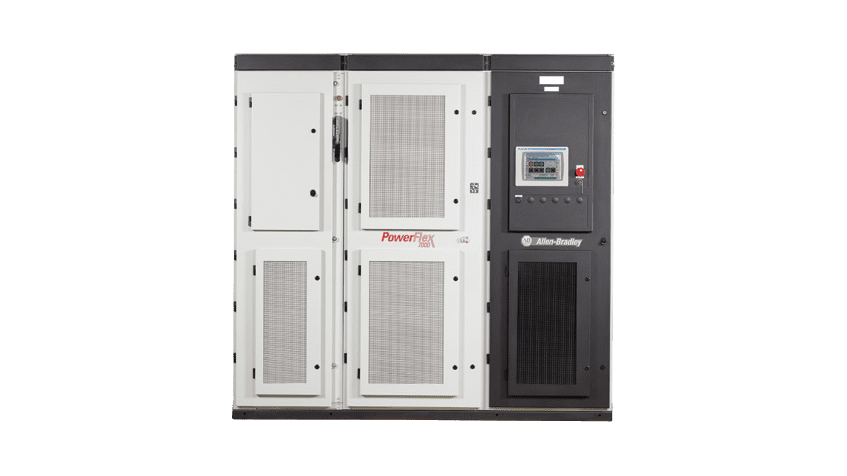
PowerFlex AC Drives High-performance solutions for a wide range of global applications
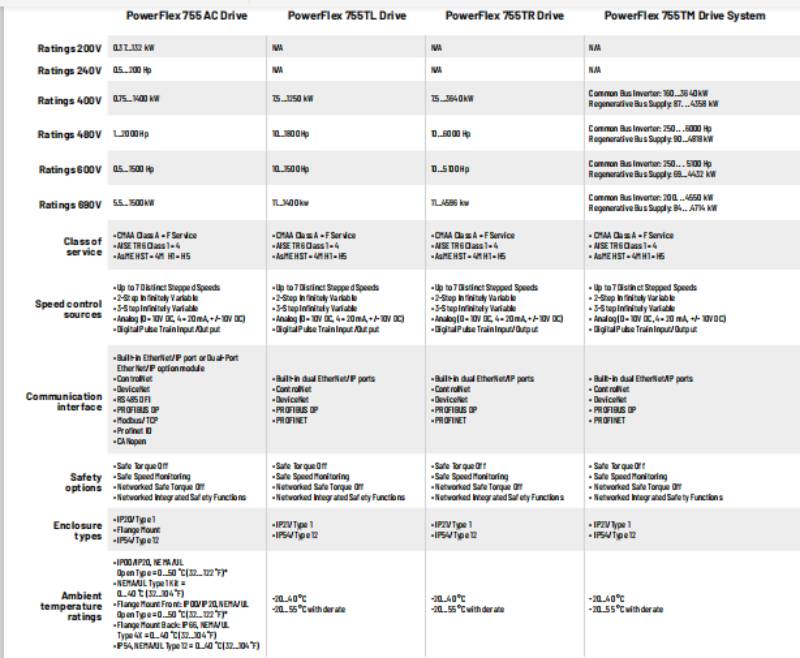
PowerFlex Medium Voltage and DC Drives. A variety of drive types to meet a wide range of applications
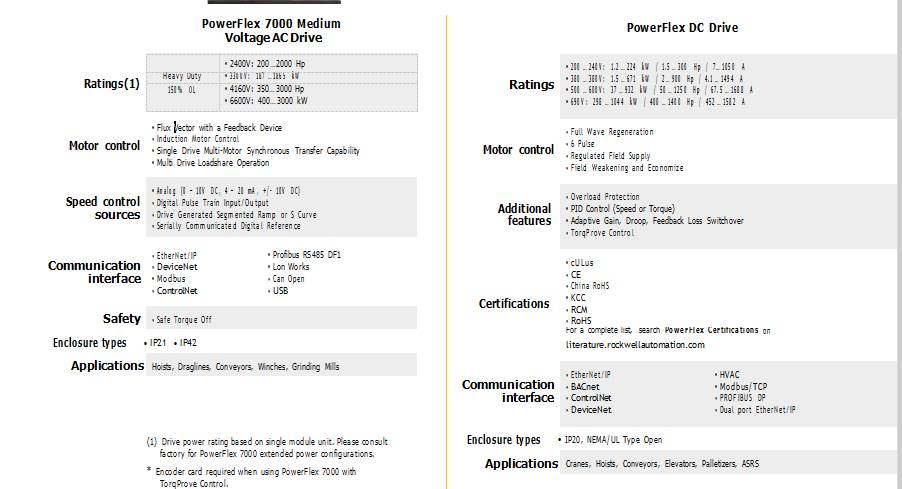