Welcome to Multivista
Through a journey of nearly five decades, Multivista has built a reputation for quality, values and service. Built on a foundation of industrial expertise, agile workforce and value-driven partnerships, Multivista has successfully served various segments of the industry.
Our two major verticals are Industrial Distribution and Print Solutions.
We offer our clients differentiated, service-driven access to products from some of the well-known industry leaders. Our print solutions combine best-in-class technology, responsible sourcing with sustainable manufacturing to deliver world-class services to global publishers.
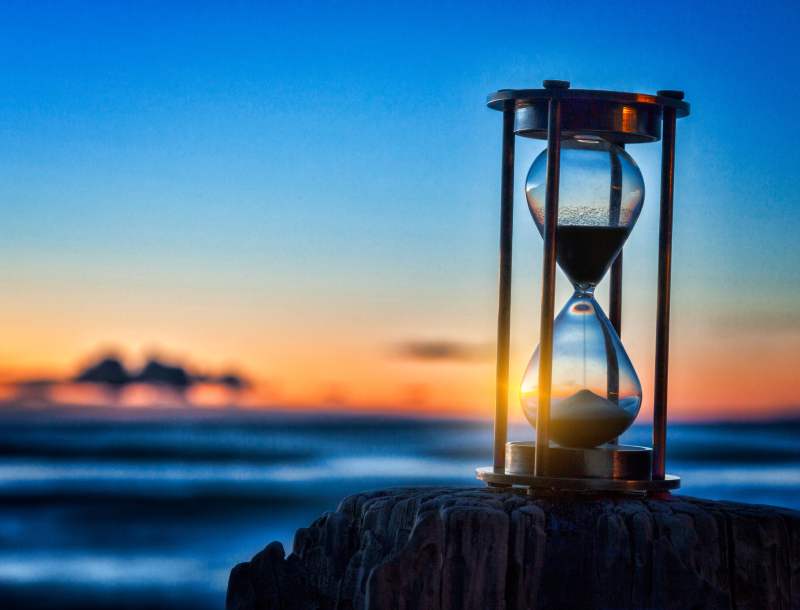
Our Businesses
Our clients trust us to bring them top-of-the-line products, powered by our association with industry stalwarts, along with services delivered by an expert technical team.
Our Partners
Times Changes Values Remain
Industry leaders with best-in-class products across categories
Industries we serve
We serve diverse industries with an ability to respond to unique requirements while adhering to stringent quality, product excellence and delivery timelines.
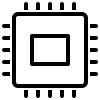
ELECTRONICS

POWER
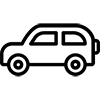
AUTOMOTIVE
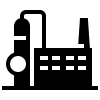
MANUFACTURING
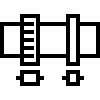
CEMENT
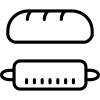
FOOD & BEVERAGE
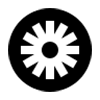
TYRE

TEXTILE
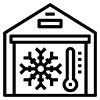
COLD STORAGE
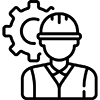
GENERAL ENGINEERING
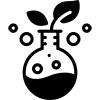
LIFE SCIENCES
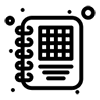
DAIRY
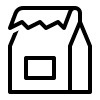
FOOD PROCESSING
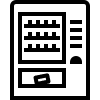
MATERIAL HANDLING
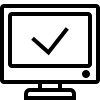
SYSTEM INTEGRATORS
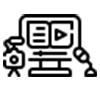
OEM




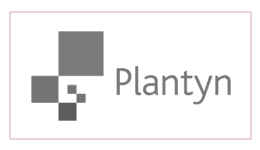
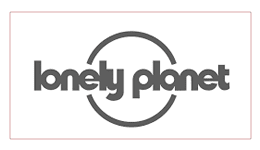

